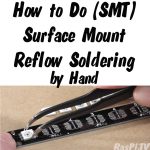
I usually assemble my own prototype PCBs in my workshop. For traditional through-hole technology (THT) and large surface mount (SMT) this is a straightforward matter with no special equipment required – just a soldering iron and regular solder.
But, as the boards get more complex and with smaller surface mount parts, you have to shift your methods to something more suitable. For my RasPiO InsPiRing prototypes I’m using 0603 sized capacitors. These are too small for me to be able to do efficiently by hand with an iron. Also the pads on the APA102 LEDs are really close together. So in this case I used more or less the same technology that is used in full-scale production…
- Solder paste
- Metal stencil
- Hot air to melt the solder
But I don’t have a reflow oven, so I use a hot air rework station (I call it a reflow gun – which is probably not offically correct, but who cares?)
I’ve made a video showing you how I do it. The actual pick and place and soldering are both in real-time. The video shows you exactly how long this process takes. I hope you’ll find it interesting. I really enjoyed making this one and want to do more of this sort of video if people find them interesting. The video is ~20 minutes long but I think you’ll enjoy it.
Oh and don’t forget to check out RasPiO InsPiRing as well.
That was really interesting, thanks Alex! The sort of stuff you never normally get to see :-)
Would there be any reason not to stick some sort of small “positioning blocks” on the back of the stencil, that the PCB would then slot between? Or would that be too inaccurate (wobbly?) and work less well than double-sided tape?
You can do that. In fact I have done exactly that before with other boards. I used four PCBs of the same thickness as the board being stencilled. It works well, but takes a while to set up right. But it does give you a cleaner ‘release’ and consequently less clean-up of the solder paste afterwards.
It was fun watching the solder paste ‘magically’ transform from grotty grey goop into super shiny silver ;)
Yes it’s a pity I couldn’t get the camera to focus any closer. Would be great to do a close-in view of that.
Great video, thanks. Where do you get the stencil from? Is it an option when you order a PCB?
Yes stencil is an option when you order a PCB. Also in your PCB design software you need to ensure that the “paste mask” layer is enabled so that a Gerber file is generated for it. Stencils cost extra, but well worth it. The job would be much harder without one. You can also get laser-cut acetate stencils for about £15.
Thanks for the sharing!
BTW, if you have a hot plate, you can use it for reflow. That way you can free your both hands and hold the camera closer. That will be very interesting :-)
The camera won’t focus any closer, sadly. I always use a tripod. It would be horribly shaky if I hand-held.
You’re really good at hand-holding in your RasPi.TV and RasPiO tutorials and instructions though Alex :-) I mean that in a nice way.
Haha, I’ve just noticed how similar RasPiO looks to RasPi0 (Ras Pi Zero) BTW. Always ahead of the curve!
Yes someone tweeted a question at me the other day containing both RasPiO and RasPi0 and expected me to see them as different things. Probably the least likely person on earth to spot that when it’s my own brand. :)
It’s a good thing you’re not involved with https://pythonhosted.org/RPIO/ ;-D
Wow! That was so cool watching the heat gun melt and secure each cap and LED. I could actually see the solder melt and solidify as you went from LED to LED. And moreover, it actually worked. Fantastic! I think I am going to have to save up and get a soldering rework station similar to yours.
Thanks Rusty. The one I bought is hobby-rated which is fair. Industrial grade stuff is a lot more expensive but more robust. I don’t use the reflow gun an awful lot, but it’s there when I need it and very useful when I do. I do use the soldering iron a lot though. I reviewed it here three years ago and CPC still sell them (~£131)
Review: https://raspi.tv/2014/a-quick-look-at-my-new-soldering-rework-station
CPC link: http://cpc.farnell.com/tenma/21-10130-uk/soldering-rework-station-esd-uk/dp/SD01741
Possibly the first time some watchers have heard ‘fiducials’. I know what you mean, but may be worth explaining.
Can you link to the solder you use?
What do you do if you don’t have a stencil?
See https://raspi.tv/2014/a-quick-look-at-my-new-soldering-rework-station ;-)
Couple of years ago, I built several identical boards using an Atmel XMEGA 64-pin IC.. Managed to solder the chip by hand (plus a much smaller 8-pin philips/NXP logic level converter). Few tips: Get a cheap pair of x3 reading glasses. Buy a flux pen (pricey at €15, but soldering’s sooo much easier. ) Good set of tweezers. Loads of solder braid. Blue-tak’s your friend for holding the board on the bench. Use 0805 parts, mainly because when one ‘pings’ out of the tweezers, better chance of finding it!
Bought a hot-air reflow machine, never used it!
It would be nice to see a tutorial like this on how to solder one of these SMT GPIO connectors (https://www.adafruit.com/product/2187) to a RPi0. They don’t exist anywhere, and I’m at a loss as how to go about it. :)
It’s the wrong part for the job. There are meant to be rectangular pads to attach those ‘feet’ to, not through-holes. It might be possible, but why? If you want a female header on your Pi zero, why not buy a through-hole one?
Space.
When trying to keep the board that the Rpi0 is connecting as close to the board as possible, as to be able to fit into an already predefined space (in this case… a case).
More specifically, I’m trying to get it so that I can reuse or swap out the RPi0 with a PSPi v4 board as needed (see this link for details on PSPi https://othermod.com/pspi-1000-version-4/).
I would imagine that other projects would want to save as much space as possible… somewhere… right? This seemed like a good solution.
If not, would you have a similar/better solution in mind that would sit as low as this?
I think I found a solution to my own question. I found a header with straight pins… which I hadn’t been able to find before: https://www.adafruit.com/product/2243
Thanks for your input… It helped to point me in the direction I needed :)
OK well in that case, I’d suggest trying to bend the ‘feet’ so that they fit in the through-holes (if they’re not too wide) then soldering in the ‘normal’ way.
If you’re spending over $100 on that PSPi board (which I hadn’t seen before, but looks neat) then it probably doesn’t add too much extra to spend $5 or $10 on another Zero or ZeroW so that you can just solder it in place (as designed) and then not have to worry about being able to swap it in or out? ;-)